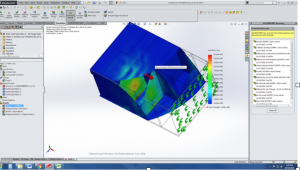
The past few weeks, the team had been working on wiring the electrical systems for racecar, “Thor”. This had been a major repeated issue for many years, and we hope to solve our issues with our car’s electrical systems this year.
We had also drew the wiring diagram for the low voltage box. In previous years, a graduated graduate student built an electric racecar called Epsilon. Though it was only for a project, and therefore not built with the FSAE regulations in mind, it still serves as a good example for us to base Thor’s electrical system off of. One of them was the driver’s display. This tells us the car’s speed and voltage in the battery. We have planned for Thor to have an identical system to simplify things.
Our battery boxes are also in development, though only existing as Solidworks constructs at the moment. We have planned on constructing them out of steel, and welding the corners together. Last year, they were two separate boxes, and fitted together with rivets. The problem was that this was extremely time consuming, and also horrendously heavy. By only using one box, we simplify construction, and also allowing us to store the batteries in the back. This should hopefully shorten the car a bit, though center of gravity may still be an issue. Welding is also a lot quicker that using a few hundred rivets. These boxes need to withstand a lot of force, up to 40Gs in some places.
These, of course, are going to be used to power our electric motors, which have been supposedly taken from a golf cart. We geared it down slightly, in order to provide more torque at the beginning at the cost of limiting our top speed. However, we have observed from last year that we are unlikely to reach that high of a speed anyways.
Huh, I ramble a lot when I get going. Good night everybody.
-Ethan “Appletank” Cheng.